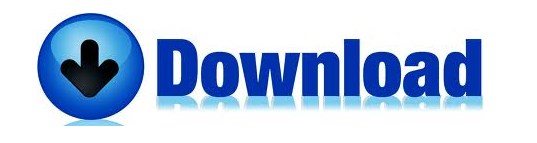
The relationship used most readily today is the direct proportionality between stress and strain. Though his "law" was established for the case of springs alone, it has since been related to all materials of known surface area. More than 300 years ago, Robert Hooke identified a proportionality that has remained a fundamental concept to physicists and engineers to this day. After the activities, the lesson concludes with a stress-strain quiz to assess each student's comprehension of the concepts. Through the lesson's two-part associated activity, students 1) explore Hooke's law by experimentally determining an unknown spring constant, and then 2) apply what they've learned to create a strain graph depicting a tumor using Microsoft Excel®. First they learn the governing equations, then they work through several example problems, first individually, then as a class. SEE IT ON TWITTER Engineered sheet metal forming lubricants save money, improve performance, and are better for the environment.Students are introduced to Hooke's law as well as stress-strain relationships. SEE IT ON TWITTER Concrete? There's no opportunities for improvement there, right? WRONG! Today's materials engineers influence all manufacturing - even on materials created 2500 years ago. SEE IT ON TWITTER Tesla has taken delivery of the world's largest casting machine, which will consolidate 70 parts into one casting.
#Engineering stress vs true stress pdf free
Join us for this free virtual event from Precision Metalforming Association and SEE IT ON TWITTER I'm teaming up with Eren Billur (畢艾隆) to present an overview of Recent Developments in Warm/Hot Stamping. SEE IT ON TWITTER Join us Tuesday, 5 October for this free webinar and learn about the recent developments in press hardening steels and warm/hot forming of aluminum alloys! SEE IT ON TWITTER Congratulations to Jayanth Chintamani and colleagues at ArcelorMittal for the successful development of #3rdGen #steel used in the upcoming Ford Motor Company Bronco! 980MPa + 20% elongation = great combo! SEE IT ON TWITTER Great article written by Eren Billur (畢艾隆) on the history of press hardening steels in automotive applications within. You will learn so much, and gain an appreciation for SEE IT ON TWITTER An excellent read, and if anyone want to know more about auto body construction, you should follow Daniel Perez. Where “s” and “e” are the engineering stress and strain, respectively, and “ σ ” and “ ε ” are the true stress and strain, respectively.Īnd check out for a plethora of information about Advanced High Strength Steels! Brought to you by The relationships between engineering values and true values are: In circle grid analysis, engineering strain is the percent expansion of the circle compared to the initial diameter of the circle. It is, however, a much better representation of how the material behaves as it is being deformed, which explains its use in forming simulations. Unless thickness and width are being monitored continuously during the test, you cannot calculate true stress. At any load, the true stress is the load divided by the cross-sectional area at that instant. While you are pulling, the length increases, but the width and thickness shrink. At any load, the engineering stress is the load divided by this initial cross-sectional area. It’s easy to measure these, since it is your starting material.
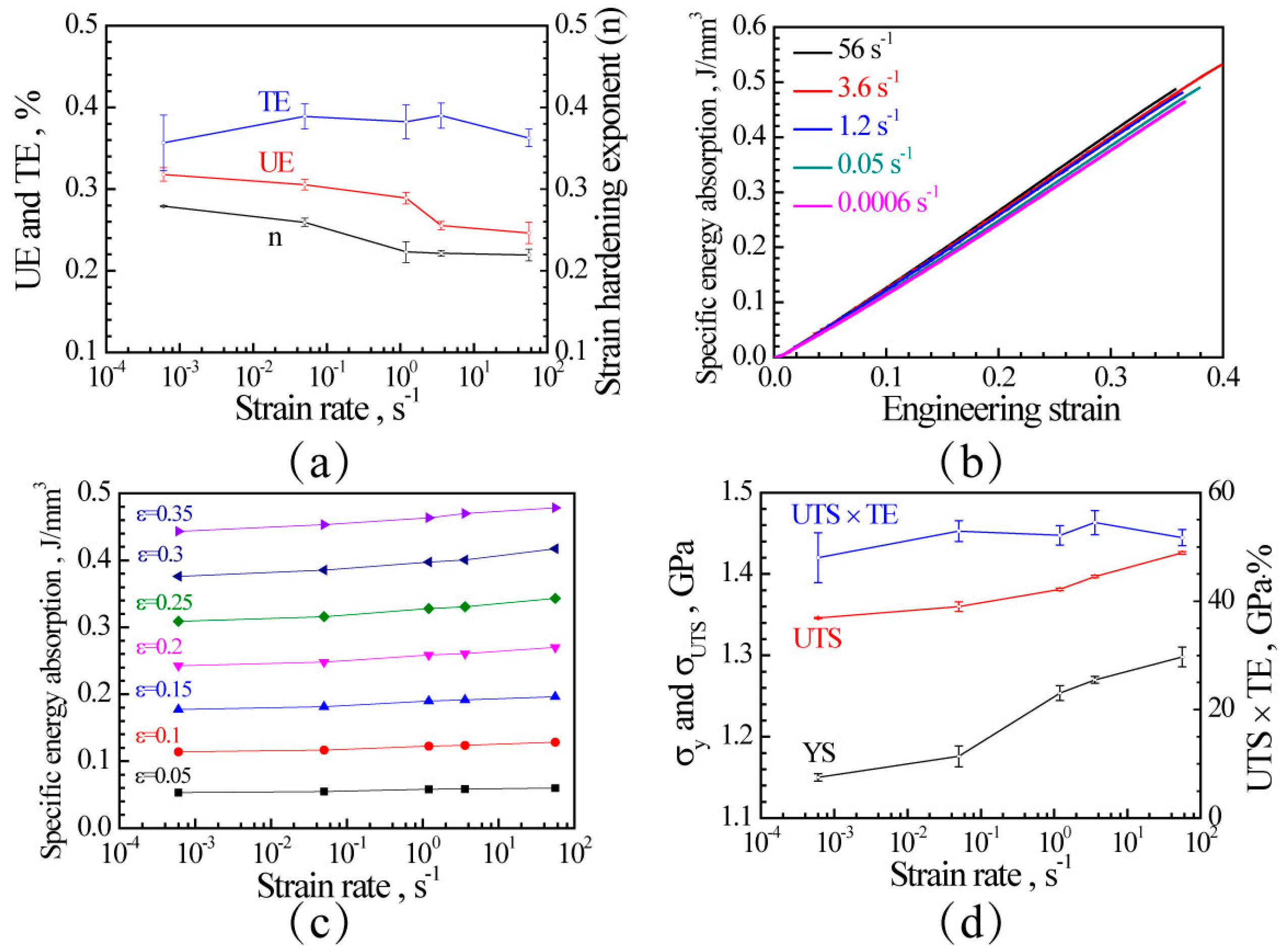

But what cross section are you considering? Before starting that pull, the bar had a known cross-section of, let’s say, 0.5″ wide x metal thickness. Load divided by cross-sectional area is force, or stress.
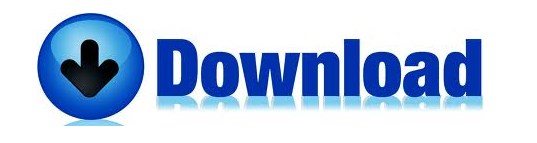